MANIFATTURE LOMBARDE progetta e produce borse di alta gamma e accessori in pelle e tessuto. In 40 anni di attività, ha consolidato significative e originali maestrie artigianali nella lavorazione del pellame, tanto da consentirle di vantare ad oggi collaborazioni con alcune tra le più illustri e glamour Maison francesi, americane, italiane e asiatiche. E’ stata fondata da Claudio Budel nel 1971 calcando le orme di antiche tradizioni familiari di maestri pellettieri italiani. L’azienda ha la propria sede e i propri laboratori di produzione a Milano tenendo fede all’incomparabile valore rappresentato dall’artigianalità e creatività del made in italy.
PROGETTO: Digitalizzazione dei processi, tracciatura della filiera e controllo delle scorte
Come abbiamo risolto l’esigenza del cliente ?
L’azienda stava attraversando una fase di forte crescita ed aveva la necessità di velocizzare i processi, tracciando tutte le informazioni scambiate tra i reparti oltre che con le Maison ed i propri terzisti. Dagli acquisti alla produzione passando per la Fatturazione e la gestione degli RMA. Un’ altra esigenza fondamentale era quella di standardizzare il processo produttivo, nonostante i clienti gestissero in maniera diversa articoli e prodotti finiti, con richieste e necessità assai difformi (ad es per la fatturazione: chi per fasi, chi per prodotto finito, chi in conto lavorazione).
Con la forte crescita era sorta la necessità di ottimizzare gli acquisti delle materie prime e minimizzare le giacenze, era quindi necessario gestire gli approvvigionamenti dei materiali in base ai relativi tempi di consegna, per non dover fermare mai la produzione per mancanza di materiale. Inoltre si voleva tracciare i lotti e tutte le altre particolarità dei pellami, in modo da sapere cosa vi fosse esattamente contenuto nella singola borsa completata.
Il processo che è stato implementato è il seguente:
1. Arriva l’ordine della Maison (manuale o in semi/automatico dal rispettivo ERP, SAP, AS400, NAV)
2. In base al Brand vengono generate le schede dei prodotti finiti in automatico o in manuale (collegate eventualmente alla prototipia, o al CAD)
3. In conformità alle distinte base, vengono generati gli impegni del materiale (da acquistare o da ricevere in c/to lavorazione direttamente dai committenti).
4. L’ufficio acquisti si occupa dell’approvvigionamento del materiale da acquistare (avendo a video pannelli di controllo per ordini automatici, gestione di listini evoluti per data e/o qtà, scelta e taglie dei materiali).
5. Arriva la merce (acquistata o in conto lavorazione), viene fatto il ricevimento e registrato il ddt a sistema (il ddt si aggancia agli ordini fatti ai fornitori nel passaggio precedente, oppure alle attese di materiale in c/to lavorazione).
6. Il personale del magazzino carica la merce fisicamente, tramite lettura di barcode codificati nel gestionale, con tutto il tracciamento della location dove viene stoccata e di chi sia il proprietario (Manifatture se acquistato, o il singolo cliente se in c/to lavorazione).
7. Il personale della produzione “lancia” gli ordini (cioè li mette in produzione) ed invia al magazzino le liste di prelievo merce.
8. Il personale del magazzino preleva la materia prima, i semilavorati o i prodotti finiti e li invia alla relativa destinazione (centro taglio, artigiani esterni, cliente, fornitore) a seconda del ciclo produttivo della commessa. Ad ogni movimento della merce o stato di avanzamento di una fase del ciclo corrisponde anche un passaggio virtuale di merce tra i vari magazzini e il WIP, in modo che tutto venga valorizzato con la massima precisione e senza perdersi alcun passaggio.
9. A seconda degli accordi con i clienti, alla fine di una fase può scattare la fatturazione per SAL e/o la comunicazione verso il cliente dello stato avanzamento lavori. Quando il singolo prodotto è terminato, viene caricato in magazzino, tracciando di fatto anche tutto il materiale di cui è composto ed il report corrispondente che verrà poi inviato al cliente.
10. All’interno dei processi di movimentazione, si è realizzato un workflow di spunta elettronica dei ddt dei fornitori, in base al quale l’amministrazione e l’ufficio acquisti possono vedere se quanto ricevuto corrisponde esattamente a quanto è stato ordinato e anche alla ricezione della singola fattura elettronica dallo SDI, in automatico essa viene collegata e confrontata con ordinativi e ddt per verificare se ci siano difformità.
Anche la fatturazione attiva è tutta guidata dal sistema, e si differenzia in base agli accordi contrattuali coi clienti, che sono ovviamente inseriti a sistema e agganciati al ciclo produttivo.
11. Oltre a ciò, è stata implementata tutta la gestione dei resi ai fornitori/terzisti/committenti (sia di prodotto finito che dei singoli materiali o semilavorati).
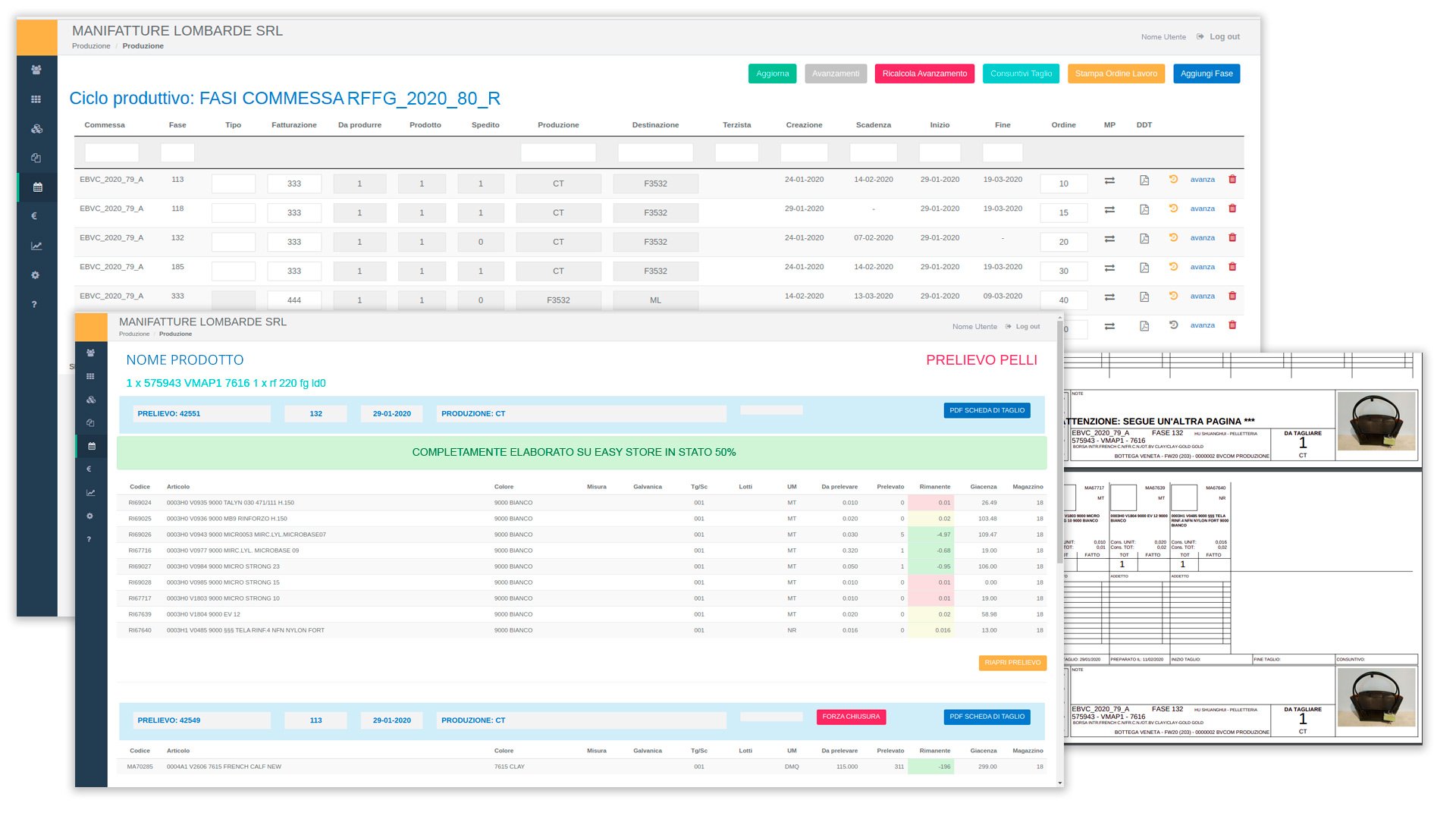
Quali risultati ha ottenuto il cliente ?
Digitalizzazione completa di tutto il processo produttivo, notevole riduzione dei magazzini utilizzando la logica del just in time, si è raggiunto quasi l’azzeramento degli errori manuali (o cmq quei pochi vengono immediatamente rilevati), la contabilità di magazzino è diventata pressochè automatica e gli inventari (anche intermedi) non sono più un problema, inoltre si è riusciti a scalare in maniera verticale senza problemi, con la perfetta integrazione di buona parte degli ERP esterni (AS400, Sap, Navision ecc.) sia verso clienti che fornitori e coi sistemi di progettazione 3D in uso ai progettisti, interni.
Questa integrazione è durata 2 anni, ad inizio del progetto la società contava circa 30 dipendenti, oggi è distribuita su 3 sedi con più di 120 collaboratori.
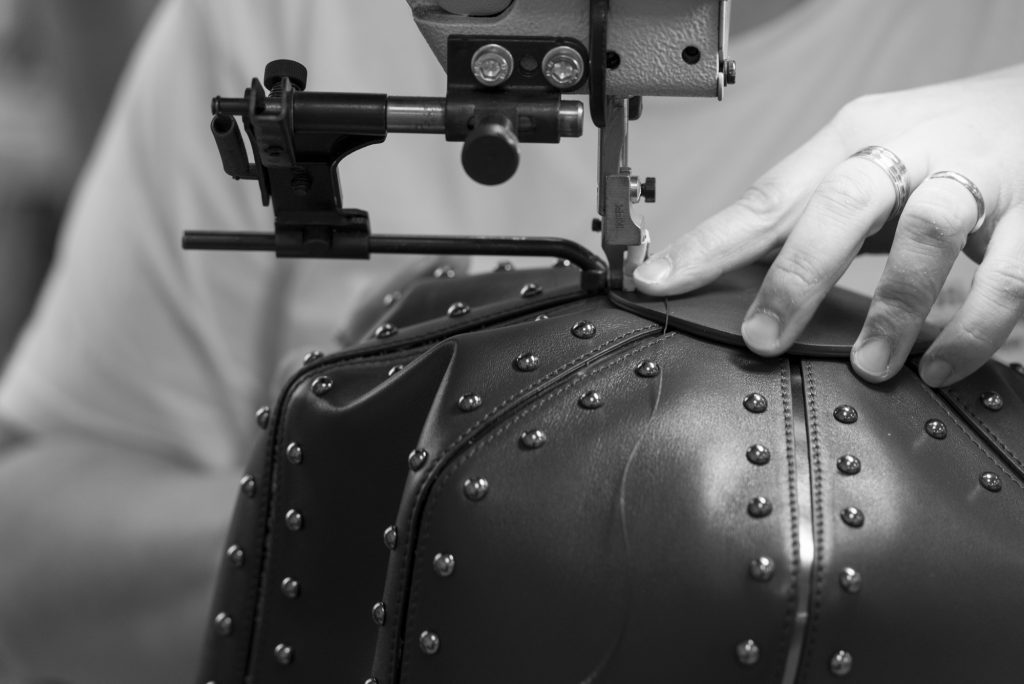
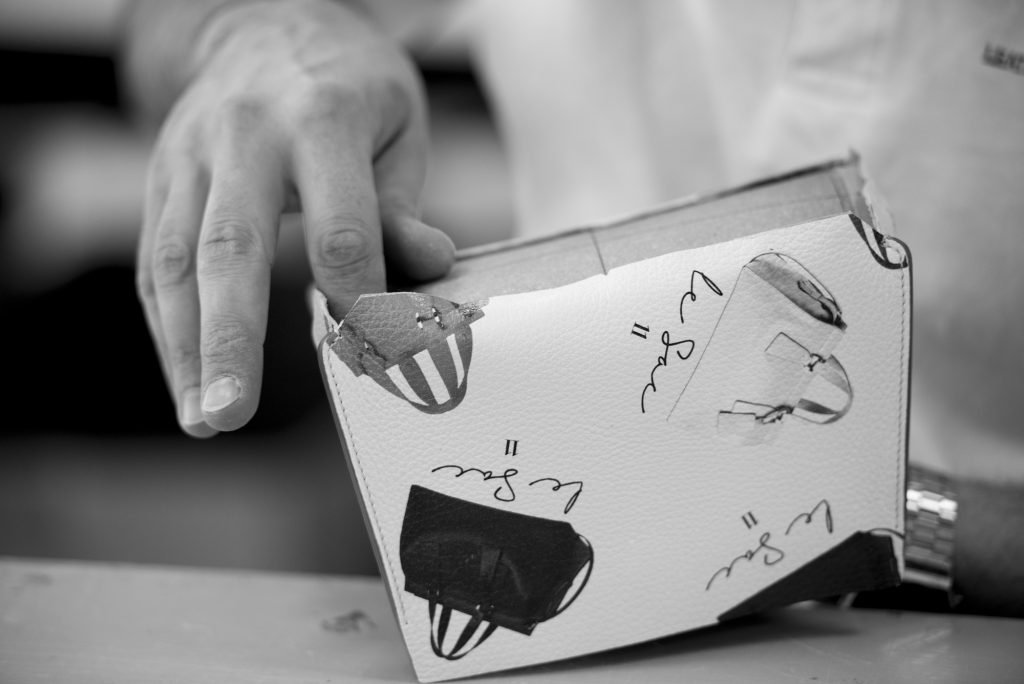